Jon Miller, of Kaizen Institute, let us know that FastCap will be included in his next book titled Creating a Kaizen Culture: Align the Organization, Achieve Breakthrough Results, and Sustain the Gains. Cool!
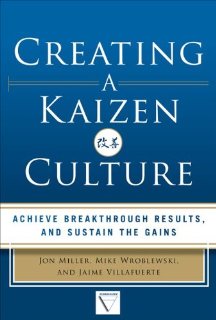
Below is a draft excerpt:
Growing People Every Day at FastCap
FastCap is a product development company based in Bellingham, Washington, USA. Established in 1997 by Paul Akers, a veteran woodworker and inventor, FastCap engages its entire workforce of thirty people in the maintenance and improvement of standards every day. There are several notable features to the kaizen culture at FastCap. The company culture would not be what it is without the unique passion, urgency and energy of Paul Akers as a leader. As an inventor, Akers is never satisfied, always finding something in the world that does not work and inventing a solution. This makes Akers a demanding leader, a tireless teacher and for the unprepared, an exhausting source of ideas. When Akers found kaizen, he found a way to help everyone in his organization see the processes in his company in the same way that he saw the word: always something to improve. In order to make it as simple as possible for people to understand and immediately take action, Akers demanded that everyone make a 2 second improvement every day. He wanted to engage every person’s mind at FastCap in finding something that could be improved, no matter how small. Akers even wrote a 100-page book about this approach titled 2 Second Lean: How to Grow People and Build a Fun Lean Culture to share the story. Akers commitment to developing his people into problem solvers who are aligned with his vision and who understand the process takes the form of the daily morning meeting. Every day, for thirty minutes, every FastCap employee stands in large circle in the middle of their facility. They review the mistakes that were made on the previous day, the reason why and what can be done to prevent similar mistakes in the future. They engage in peer-to-peer teaching, rotating a different employee as the teacher each day. They watch a video to learn about history and discuss its lessons. They start their day as one team.
A simplistic cost calculation would show that the daily 30 minutes of non-productive time for 30 people at $30 per hour on average time 220 days equals $100,000 per year. How can a small company possibly afford this? Paul Akers would say, “How can you possibly afford not to?” FastCap ships a high volume of orders and we have no doubt that the two seconds of savings per person per day easily adds up to far more than the cost of the morning meeting. Although kaizen is an improvement to the standard, and thus a self-funding activity, this is not the right way to calculate the cost and benefit of daily kaizen. There are many indirect benefits of their kaizen culture which lower costs and accelerate growth at FastCap, but are much harder to calculate, such as:
· A positive, fun, engaged workforce in a family atmosphere
· Prevention of errors, avoidance of repeating errors, a quality mindset
· Ease of gaining top talent by becoming an employer of choice in the region
· Development of future leaders with deep knowledge of the company
· Increasing international exposure FastCap and its products through excellence in kaizen
No doubt many readers will remain in shock and dismiss out of hand the possibility of having the entire production team, much less the entire company including its President, meet every day for 30 minutes for learning and improvement. Yet how many hours each day do people in your organization spend in meetings in which zero learning and zero improvement happens? How far away from the actual workplace do these meetings take place? How fresh or accurate is the information being discussed at these meetings? How many times was the information transferred from point of occurrence to the reporting point at the meeting? What causes such meetings to be necessary? If we view the daily kaizen activity at FastCap as a countermeasure to certain management challenges, and reflect on the situation within our organizations, we can find the answer. In the broadest sense, we can view the daily morning meeting at FastCap as the ultimate act of maintenance of standards. Each morning they confirm their commitment to the company, to each other through the history lessons and peer-to-peer teaching, to the customers through quality reviews, and to their many shared cultural values. The cost of trying to manage and repair broken processes that would result from stopping the daily maintenance would be far greater than thirty minutes times thirty people.